As costs rise in developing countries, and automation eliminates the most mindless tasks, some manufacturing and service businesses are going home—but with greatly reduced labor needs.
Boston Consulting Group partner Justin Rose offers a case study: A manufacturer of stainless steel kitchen trash bins lately moved production from China to the US. That’s the sweet part of the story for Rose, who heads BCG’s North American industrial goods and operations practice out of Chicago and coauthored a book called The US Manufacturing Renaissance. The less sweet part: His client will replace 70 Chinese workers with a maximum of 10 Americans. “At this point you can automate picking out parts, putting them on a line, vehicle driving and unloading,” the consultant explains. “It takes out significant amounts of labor.”
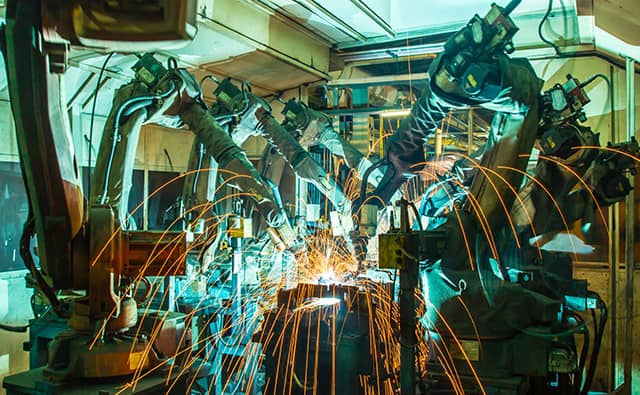
Even as Donald Trump swept to the White House on an “America First” pledge, the offshoring tide was ebbing if not turning. The US posted a net gain of 25,000 manufacturing jobs in 2016; it had averaged 220,000 lost jobs annually from 2000–2003, according to advocacy group Reshoring Initiative. European numbers are harder to pin down, but Guido Nassimbeni, who heads the officially backed European Reshoring Monitor, senses a similar shift. “Companies are looking at offshoring with less hope and fewer illusions, for several reasons,” he says.
One reason is quantifiable: rising labor costs and shortages in offshoring hotspots, such as China. Another is the hassle of managing globally. “Manufacturing overseas is much more expensive than you thought when you consider the cost of monitoring a supply chain and learning how to manage all the different legislation,” says Nassimbeni, who chairs start-up facilitator Friuli Innovazione and teaches at Italy’s University of Udine. A third is the coming next wave of automation, which Rose’s trash-bin-making client jumped on. A fourth driver is unique to the US: energy prices that have plunged this decade thanks to the shale-gas revolution.
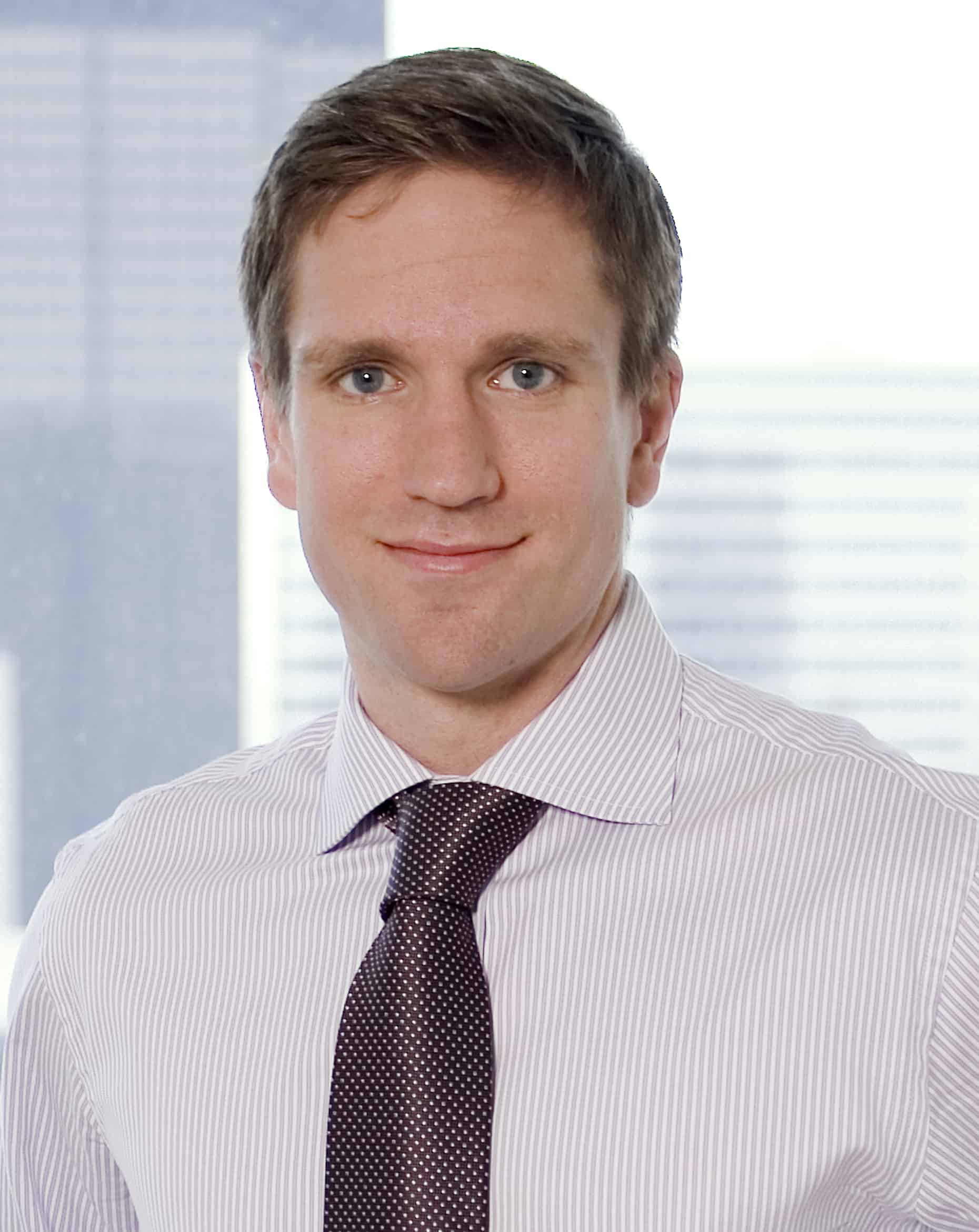
This all adds up to complex new options for managers, who can no longer simply set up shop where labor is cheapest—and a complex lack of options for politicians, who will be unable to resurrect millions of lost factory jobs even if the factories themselves reappear on native soil. A similar dynamic is seen in service industries, where wages are rising in offshore magnets like India and Eastern Europe, while software advances render obsolete many low-skilled jobs in data entry or customer service. “This is the beginning of the end of offshoring,” says Aijaz Hussain, India leader of Deloitte’s Center for Industry Insights in Hyderabad. “From now on, it will have to be really valuable” to be worthwhile.
IS THIS RIGHT FOR US?
Could reshoring be right for your company? BCG’s Rose offers a metric for manufacturers: the ratio of labor to shipping costs. Apparel and other lightweight, handwork-intensive goods will keep chasing cheaper workers. “It’s a complete illusion to believe that manufacturing can go back to Europe in terms of volume,” Kasper Rorsted, chief executive of German sneaker maker Adidas, said earlier this year, dashing reshoring hopes raised by his predecessor, Herbert Hainer.
The sweet spot for reshoring is in autos and other weighty machines, where labor accounts for less than 20% of the sticker price, Rose says. Transportation equipment manufacture brought 134,000 new jobs to the US between 2010 and 2016, almost four times the second-place category of “electrical equipment, appliances and components,” according to the Reshoring Initiative.
The second factor is the availability of appropriately skilled workers and suppliers back home, which is far from a given. “The US has a very deficient workforce relative to major competitors,” Reshoring Initiative founder Harry Moser laments. “China makes all sorts of things we don’t anymore, from circuit boards to textiles. In Germany and Switzerland, 60% of young people go into an industrial apprenticeship.” America needs a 10- to 20-year skills push before it can lure manufacturers back en masse, Moser says.
A third key is “nearshoring” possibilities, which can combine labor savings with market access and quick factory-to-customer turnaround. Western European multinationals are intertwined with the Eastern hinterland, as their US counterparts are with Mexico. But politics threatens these relationships now, as Trump takes aim at NAFTA and relations sour between the European Union and Turkey, which for decades has been inside the EU customs area, though not a member.
Technology plays a role, but its potential is not equal in all sectors. One example: The footwear industry could be revolutionized by a robot that fits laces into shoes, Adidas boss Rorsted says, but no one has invented it yet.
A different equation pertains to reshoring decisions on white-collar work. Shipping is irrelevant when the product is database management or help-desk assistance. Wage growth has slowed with the growing supply of educated graduates in key outsource countries, says Michel Janssen, Dallas-based chief of research at consultant Everest Group. India’s university student population has more than doubled since 2008, to 25 million, dampening their elders’ pay demands. “We predicted that the labor arbitrage for service outsourcing would be finished by 2015–2020,” Janssen says. “Now we expect it to be there until 2040–2050.”
At the same time, new technology can be phased in much more cheaply and quickly in services than in manufacturing: There is no plant to retool; no robots to buy; only software. That offers broad opportunity to replace swarms of offshore workers with smarter systems and a few native workers to oversee them, says Fumiko Kondo, managing director of New York–based consultant Intellilink. “There is a rapidly growing field called robotic process automation, which can be applied to anything that is transactional: processing an invoice, retrieving lost passwords or onboarding a new hire for HR,” she says. “This can address dissatisfaction with service levels offshore without increasing labor costs.”
In the broadest terms, experts say, proximity to markets and skill clusters will matter more to business over time, and the nominal cost of an hour of labor will matter less. That, of course, includes proximity to Asian markets, which are the world’s fastest growing. “Manufacturing is shifting away from one workshop for the world to clusters serving regional demand,” BCG’s Rose says.
As the technology component of both manufacturing and services increases, the geography of those industries will become more like high-tech—driven by educational institutions and like-minded collaborators and competitors. Germany, not surprisingly, is leading the European field in this effort. “They have invested heavily in a concentration of research centers and excellence centers dedicated to manufacturing 4.0,” Nassimbeni says, using a term that denotes ultra-automated production.
In the US, that process is more decentralized, Reshoring Initiative’s Moser says. “You are starting to see rural domestic outsourcing of IT and other skills,” he says. “You may have a good community college in Nowhere, Pennsylvania, that teaches coding.”
Still, no savvy observer expects a returning flood of low-skill, high-wage jobs to make America, or Europe, great again. “Work will be a problem for a long time,” Nassimbeni concludes.